HOME > Research Summaries > Development of Sensor System for Medicalwelfare
Research Summaries
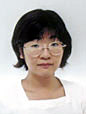
Development of Sensor System for Medicalwelfare
Mami Tanaka
Professor
Department of Biomedical Engineering, Graduate School of Biomedical Engineering
E-mail:
We are studying the development of a sensor system for medicalwelfare by using functional material as following topics.
1. Active tactile sensor system for palpation
Palpation of the finger is often used on the medical field. However, the rate of correct diagnosis is dependent on the doctor’s experiences. This research is concerned with the development of an objective tactile sensor for palpation. Polyvinylidene fluoride(PVDF) film is used as a sensory receptor. The current output from the PVDF film is proportional to the rate of the strain induced in the film. Experimental results show that the output signal from the piezopolymer film takes the form of a brief potential wave at the onset of the pressure pulse and a similar brief wave at the termination. Further, there is no response during the stationary plateau of the applied pressure. The time variation is quite similar to the signal variation of the Pacinian corpuscle which is a sensory receptor in the dermis.
1-1. Haptic finger for monitoring skin conditions
This study is a development of the haptic sensor system for monitoring skin conditions. The sensor (Fig.1) is an assembly of layered media. The base of the sensor is a stainless plate, on which a sponge rubber, a PVDF film with electrode patches, a protective surface layer of acetate film and a gauge are stacked in sequence. The sensor is attached to the forefinger and pressed against the surface of the skin. It is then slid over the skin to collect surface morphological features. The result is shown in Fig.2. The sensor output well describes the skin conditions and represents the subjective evaluations of dermatologist
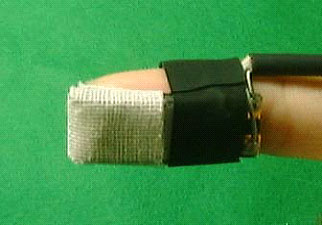
Fig.1 Haptic finger for monitoring skin conditions
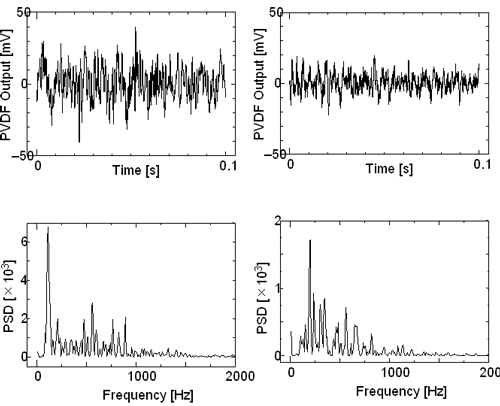
Fig.2 Sensor output and power spectrum.
(Left) Atopic dermatitis (Right) Normal healthy skin
1-2. Palpation sensor for detecting prostatic cancer and hypertrophy
Prostatic cancer and hypertrophy are diagnosed in most case by the rectal palpation using the physician’s forefinger as a detector. The two lesions are distinguished by noticing their morphological features. The hypertrophy assumes a symmetric enlargement of the prostate glands with the stiffness varying from soft to hard. The carcinoma is a hard asymmetric uneven tumor. The palpation, however, depends on the tactile perception of the forefinger, which is said to be ambiguous, subjective and much affected by the physician’s experience. This situation has drawn much interest in the development of objective palpation sensor for the detection of prostatic cancer and hypertrophy. The developed sensor well discriminates the stiffness and the various physiological states of prostate glands in vivo and non-invasively.
2. Braille letter reading apparatus
Braille is a language for visually disabled persons, in which characters are represented by patterns of raised dots so that the persons can read by the sense of touch on their fingertip. It uses a combination of six dots, in two parallel lines of three. However, learning Braille requires great efforts, especially to those acquired in the course of one’s life. To solve this problem, we have developed a tactile sensor system for reading Braille without special training by just scanning over Braille
The sensor and the sensor output are shown in Fig. 3. The shape of the sponge rubber is a right-angled triangle. The time length of contact with each dot in a vertical row of Braille varies according to the dot’s position while sensor is moved. Thus contact pattern depends on the letters.
This apparatus consists of the tactile sensor and recognition system. The sensor is mounted onto a fingertip as the wearable system and is moved over Braille manually to obtain the output. Since the unsteady movements yield variations in the waveforms, a investigation of the robust recognition system is required.
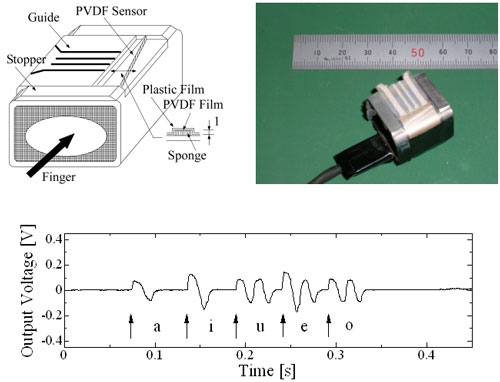
Fig.3 Sensor part of Braille letter reading apparatus and sensor output.
3) Rating and valuation of human haptic sensation
Touch is the most frequently used action to gather the information outside the body. In our daily life, various kinds of things are touched by fingers and their physical as well as morphological features are extracted and evaluated unconsciously. In the tactile function, the digital pulp of finger is pressed against the object, and then the stroke/rubbing action is started over the surface of the object to feel the texture.
It is rather difficult to handle and/or measure thin fabrics since they are very flexible. The texture of fabrics has been conventionally described by using the terminology of hand as the occupation expert uses. It is characterized by the descriptive words like “body”, “compliant” and others.
It seems that most of the force sensors developed so far have been functional to the measurement of applied force magnitude and no sensor for the evaluation of the texture of the object materials.
This study is a development of a sensor for measuring human touch sensation. To develop the system, the investigation and analysis of human touch sensation and haptic motion also has been done.
The sensor for measuring human touch sensation over the fabrics is shown in Fig.4. The sensor is mounted on the slider and the sensor is slid over the surface of the fabrics to collect the surface tactile information.
The investigation of human touch sensation by using 4 kinds panel (Fig.5) is carried out. The panels with poly-imide film are processed by eximer laser for imitating the physical properties of human hair surface. By using these panels as the target sample, human touch sensation has been investigated and the sensor system for measuring human touch sensation has been developed.
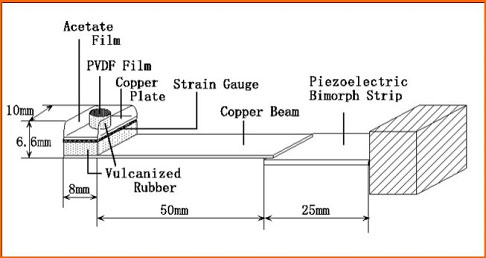
Fig.4 Sensor for measuring human touch sensation.
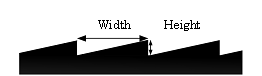
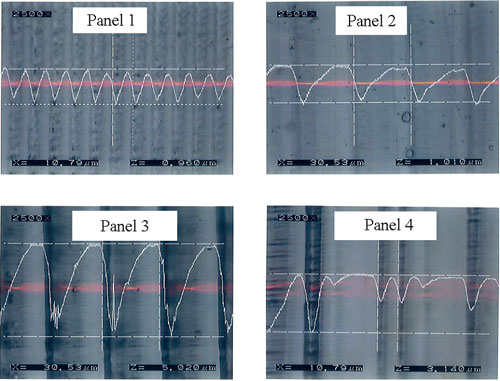
Fig.5 Panel surface for measuring human touch sensation.
Panel 1 Width 10μm, Height 1μm
Panel 2 Width 30μm, Height 1μm
Panel 3 Width 30μm, Height 5μm
Panel 4 Width 10〜30μm, Height 1〜3μm (Random)